Desalytics aim to solve Sub-Saharan water challenges with TopDutch innovation
The Dubai-based company Desalytics recently opened a WaterTech innovation hub in the TopDutch region. Its new R&D office in Leeuwarden will leverage Dutch WaterTech expertise to address water challenges in sub-Saharan Africa.
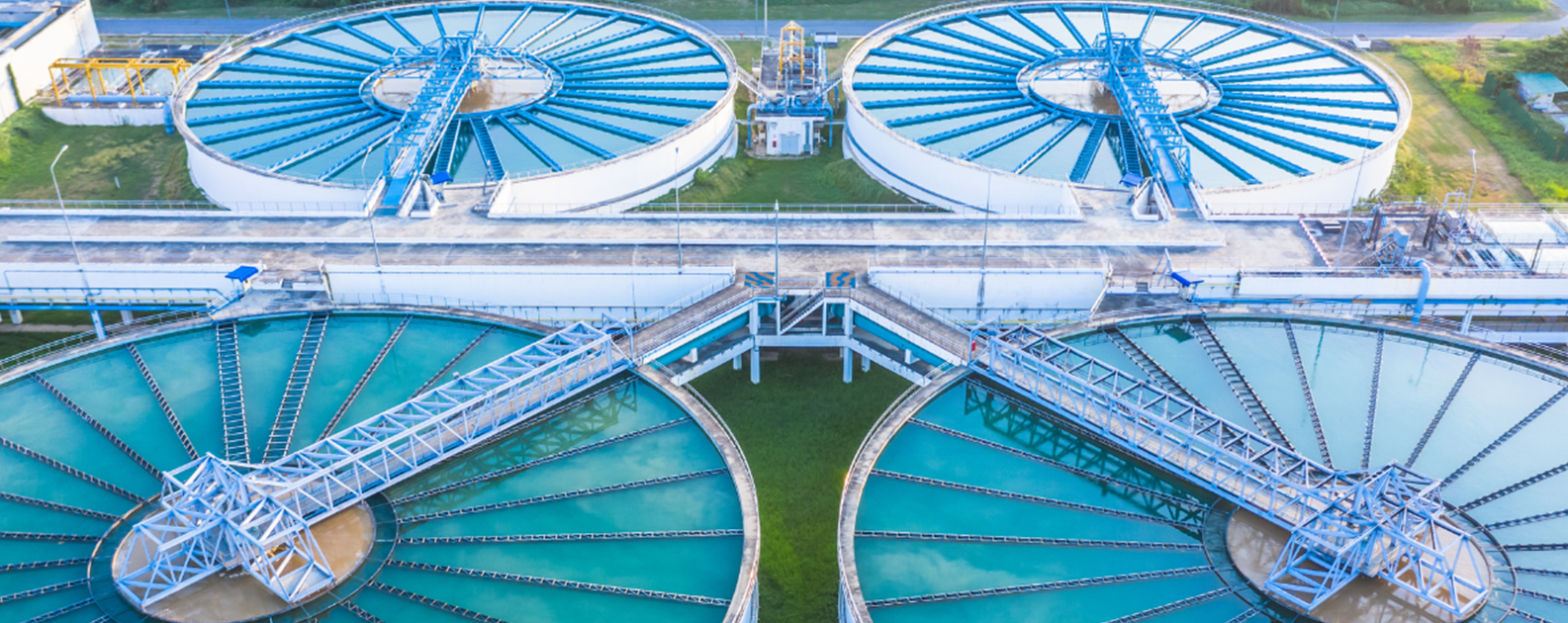
Dubai-based Desalytics, a pioneer in water quality and management innovations, has expanded into the Netherlands with a new innovation hub at WaterCampus Leeuwarden. This strategic move allows Desalytics to collaborate with leading experts and organizations in the world-renowned Dutch WaterTech ecosystem, fostering research & development efforts that can enhance its mission to provide sustainable water solutions for communities in sub-Saharan Africa.
The Netherlands is a well-established leader in water tech, supported by a strong ecosystem that encourages R&D and sustainable solutions. By joining this vibrant community, Desalytics aims to integrate cutting-edge technologies and best practices into its operations, improving its ability to address water challenges in the African continent. Together with the Netherlands, Desalytics is reshaping how water management is approached on a global scale.
WaterTech Capital of Europe
Desalytics is committed to combining global knowledge with local partnerships to provide innovative water treatment solutions. This ethos aligns seamlessly with the Netherlands’ culture of open innovation through collaboration. Through its new hub in the Dutch city of Leeuwarden, known as the WaterTech capital of Europe, Desalytics gains access to a vast network of advanced R&D know-how, industry leaders and growing startups.
In particular, WaterCampus Leeuwarden fosters collaboration among businesses, knowledge institutes and governmental entities, benefiting both Dutch companies and international players like Desalytics. By engaging with this network, Desalytics aims to enhance its impact through shared knowledge and cooperative efforts. This will enable Desalytics to pioneer innovative, sustainable solutions inspired by the Dutch water tech ecosystem, fostering international collaboration that can contribute to transforming water management worldwide.
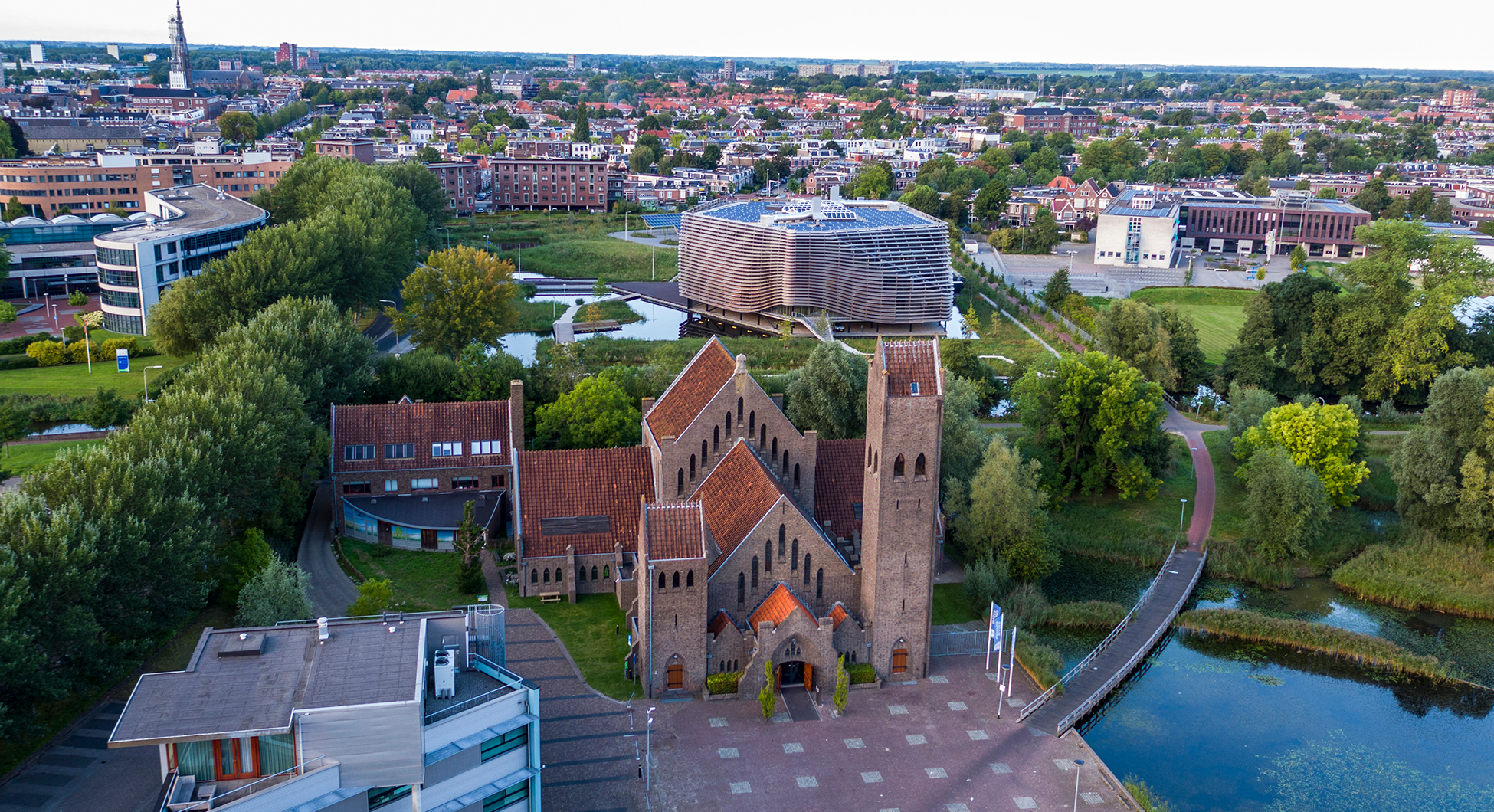
Empowering local entrepreneurs for sustainable growth
A key aspect of Desalytics’ strategy is its emphasis on empowering local entrepreneurs. By partnering with local businesses, the company disrupts traditional supply chains while promoting economic growth and sustainability. This approach enhances the effectiveness of water solutions and reflects a broader trend seen in the Dutch water tech sector, where collaboration and local expertise are essential for success.
Desalytics is dedicated to delivering high-quality water products and services tailored to the needs of municipal and industrial customers. The company focuses on optimizing processes to ensure reliable testing results and maximize returns at competitive costs. This mission matches well with the Netherlands, a country known for its effective water management practices.
Support in finding a spot to grow from
When it came time to expand into the Netherlands, Desalytics drew support from the Netherlands Foreign Investment Agency (NFIA) and its partner in the TopDutch region NV NOM, along with Dutch water tech network organization Water Alliance and the municipality of Leeuwarden. As a result, Desalytics was able to establish a strong foothold in Leeuwarden. Now with its innovation hub in the Dutch water tech landscape, Desalytics is well-positioned to grow its global impact in developing sustainable water solutions for sub-Saharan Africa.
“We are very pleased with Desalytics setting up its Dutch subsidiary at WaterCampus Leeuwarden,” says Reinder de Jong, Project Manager at N.V. NOM. “We enjoyed working with Desalytics, together with our NFIA colleagues, in supporting them to set up their activities in the Netherlands and will continue to do so. Desalytics will collaborate with multiple organizations at WaterCampus Leeuwarden and therefore contribute to further strengthen the ecosystem for water technology companies”.
Call me back
Please feel free to fill out the “Call Me Back” form below, and we’ll be delighted to get in touch with you at your convenience.
These cookies are used to optimize performance and functionality of the website. These cookies are not essential when browsing the website. However it is possible certain elements on the website will not function properly without the cookies.
These cookies collect data that we use to understand how our website is used and perceived. These cookies also help us to optimize the website for the best user experience.
These cookies allow ad-networks to monitor your online behaviour so they can display relevant ads based on your interest and online behaviour. These cookies also prevent the same ads from being displayed over and over.